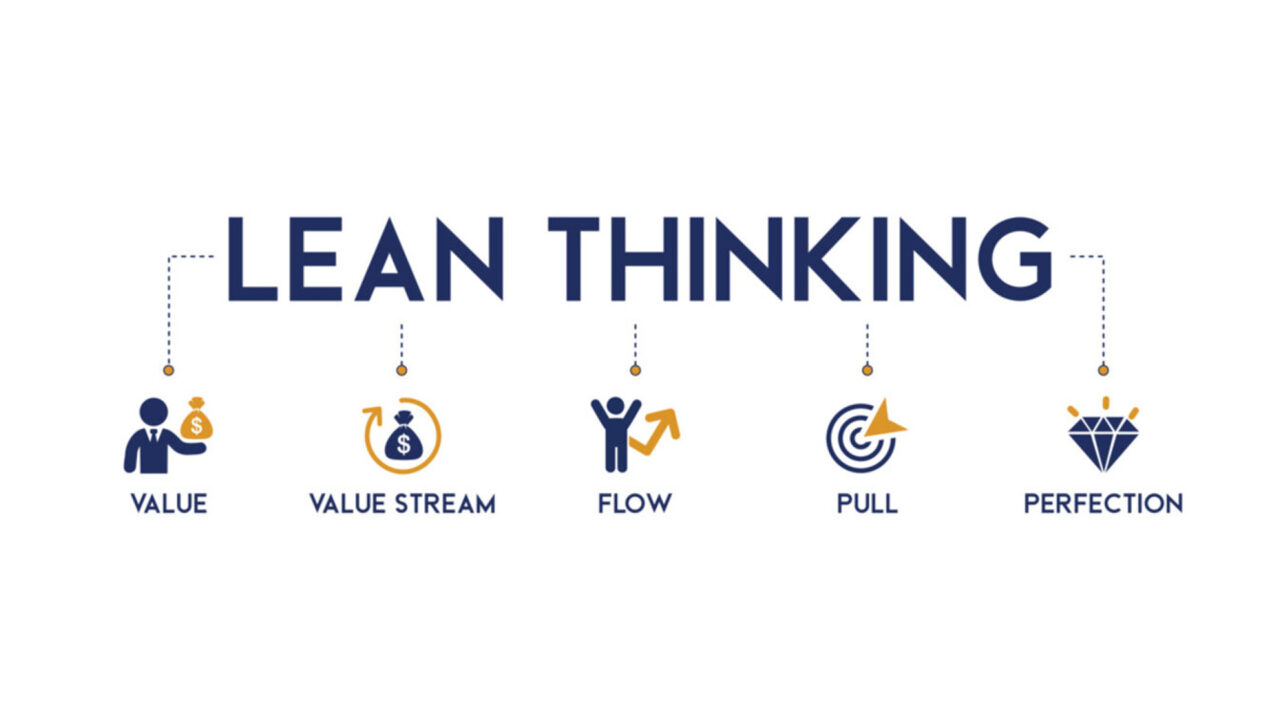
Lean thinking is a project management mindset that focuses on reducing waste, created originally in Toyota Production System (TPS) to create customer value and seek continuous process improvement. This is achieved by applying lean project management principles, techniques and tools. And Agile and Scrum management are a subset of lean thinking.
It is also called lean manufacturing or lean production, Lean techniques are just-in-time (JIT) delivery that can be universally applied for project improvement, Lean Thinking and Management principles can help your business projects gain efficiency, effectiveness, and competitive values.
Lean Thinking 5 Principles that are Applied to Optimize Projects Management:
- Value: you need to define what is the value that the customer needs. Once the customer defines what is valuable to him/her, to create a product that has only what is necessary, and remove all the unnecessary work and components it has.
- Value Stream Mapping: you need to visualize each step in the project process to identify waste and ways of improvement.
- Create Flow: you need to improve the project process flow, where you can reduce your production lead time.
- Pull System: it consists in starting new work only when there is customer demand for it. Just-in-time delivery (JIT).
- Continuous Improvement: you need to constantly use lean techniques to find and eliminate waste.
The 7+1 Types of Waste in Lean Thinking and Lean Management:
- Inventory: Having an increase in the inventory (or input) can lead to increased time in the project processes.
- Waiting: This waste type occurs when employees can’t work because they’re waiting on materials or equipment, or in the opposite case, there can be idle equipment waiting on maintenance.
- Defects: Having bad quality results is a waste that must be reduced as much as possible. it can affect customer satisfaction and increase costs.
- Overproduction: it leads to increase output results and that is why the just-in-time delivery (JIT) method is only producing on demand.
- The unnecessary motion of resources: changing roles creates waste in project processes.
- Unnecessary transportation: Unnecessary transportation of employees and tools is a waste that must be eliminated by optimizing the environment of the project.
- Over-processing: This waste consists in adding features to a product of the project that are out of scope, which makes them unnecessary.
These waste types were developed by Taiichi Ohno, chief engineer at Toyota, for the Toyota production system (TPS).
Lean thinking experts have Created an eight-waste type called “unused talent or ingenuity”, which occurs when employee’s opinions are not taken into consideration when identifying waste types, the employee’s feedback is important due to facing issues every day and employee’s thoughts can be very helpful in improving project management.
These Waste Types can be grouped into 3 Groups, which were Created Using the Japanese Language, and They Are:
- Muda: Non-value-adding work, or project processes waste. Therefore, lean maximizes value, minimizes necessary waste, and removes unnecessary waste.
- Mura: Unevenness, or waste due to inequality and balance in separating project process.
- Muri: Overburden, or waste due to trying to do too much at once.
Some Lean Thinking and Lean Management Tools:
- Jidoka: Automation with a human touch.
- Kaizen: Continues improvement.
- PDCA (Plan, Do, Check, Act): 4-steps management method for continuous improvement.
- Root Cause Analysis: finding the deep reason for the production problems (ask why 5 times)
- Kanban (Single Card): Visualizing project workflow using cards on Kanban board.
- SMED (Single Minute Exchange of Die): moving from one project process to another fast.
- Poka-Yoke: avoid unexpected surprises.
- 5S (Sort, Set in order, Shine, Standardize, Sustain): a workplace organization methodology.
Lean Thinking and Lean Management Benefits:
Reducing or eliminating waste is essential to lean project management, but the benefits of lean thinking can change depending on each project manager. Where some project managers say it is increasing company profit, while others say it maintains improvements and create customer value, and increases customer satisfaction. But we can summarize the benefits in these 6 points:
- Improve Quality.
- Inventory Management.
- Project Process Improvement.
- Eliminate Waste in all Project Processes.
- Reduce Project Time.
- Reduce Project Total Costs.
posted by Emad Zedan on 13 Aug 2022 in Project Management, UX/UI Design